Service
Our Parts Finishing Capabilities
Whether it is CNC machined, urethane cast or 3D printed parts, to gain an accurate appearance of your final product, the prototype must undergo a rigorous post finishing process, which describes the final steps required before a product can be truly brought to life.
JX provides an integrated parts finishing service to meet your diverse needs. With our experienced in-house skills and advanced facilities, we try our best to ensure the color, texture, gloss, and surface finish of parts and exceed your expectations.

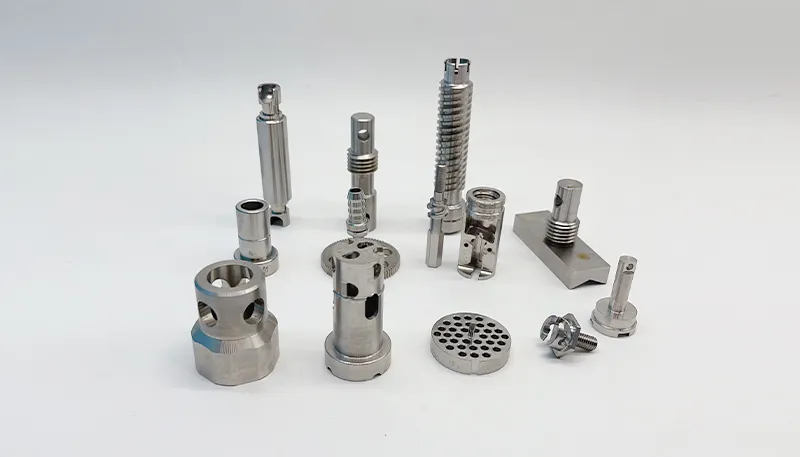

Choose The Right Post Finishing For Your Prototype Parts
JX’s in-house prototype processing is capable of providing the best post finishing, including hand-finishing, sanding, blasting, polishing, painting, and printing. We also offer a wide array of specialty surface finishing, including laser etching, anodizing, powder coating, metal plating, vacuum metalizing, chromate, chemical finishing, passivation, heat treatments, etc.
Common Post Processing
Contact us to learn more about how JX can help you with the parts finishing processes outlined below.
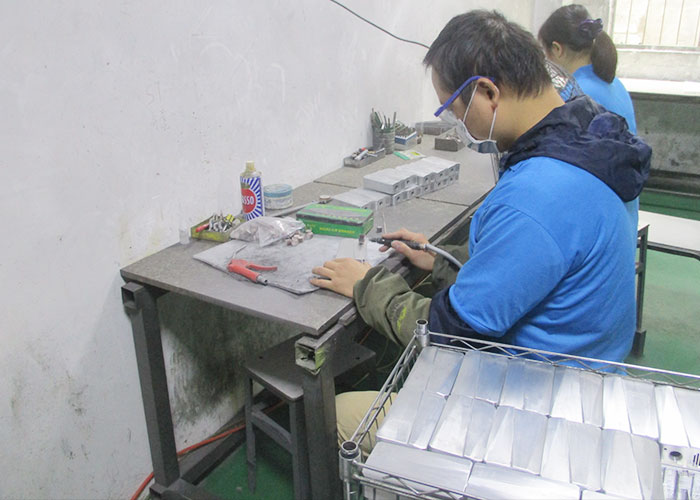
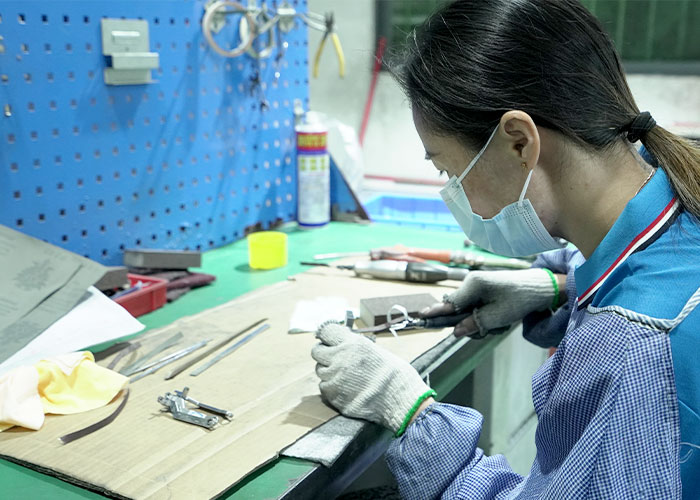
Sanding and Polishing
Smooth sanding can remove machining marks, burrs, machine lines, and adhesive marks on the surface of the parts. The flatness of the part will be improved and roughness will be reduced to create a smooth and uniform look.
High polishing process is used for a mirror finish on normal plastic, metal parts, and clear acrylic and polycarbonate parts, to achieve a precise uniform flat surface and professional-grade gloss, or to enhance the optical clarity of clear parts.
Sanded to 600 grit sandpaper surface finish is Ra 0.8 μm;
Sanded to 1000 grit sandpaper surface finish is Ra 0.4 μm;
Mirror polished and clear polished surface finish is Ra 0.1-0.05 μm.
Machined Finish
Machined parts will have marks that follow the path of the cutting tool. The machined finish is that a smooth surface, created by a machine without polishing work, only needs a little handwork to clear the bur, the part could be finished and delivered quickly soon after off the machine.
The standard machined surface roughness is Ra 3.2-1.6 μm;
The smooth machined surface roughness is Ra 1.6-0.8 μm;
The super-finished surface roughness is Ra 0.8-0.2 μm.
The finishing will increase the cost of producing a part, as extra machining steps and tighter quality control are required.


Hand Finishing
From de-flashing to gluing, filling, modifying, adding inserts, pre-fitting, measuring, and assembling, our handcraft specialists focus on every engineering detail and design specification.All post-processing is created in-house, but our team can also work with client-supplied components to finish and assemble as needed, include mating and fitting parts. Normally, this reveals engineering hurdles that are not apparent in CAD design. We will help overcome these challenges, offer solutions and achieve a finished project.
Blasting
Bead blasting adds a uniform matte surface finish on a machined part, removing the marks of tool and sandpaper. It is the operation of forcibly propelling a stream of abrasive material against a surface under high pressure to smooth a rough surface, roughen a smooth surface, or remove surface contaminants. The size of the air pressure and the size of the glass beads are the main process parameters. Glass beads come in different sizes from #80 to #220.
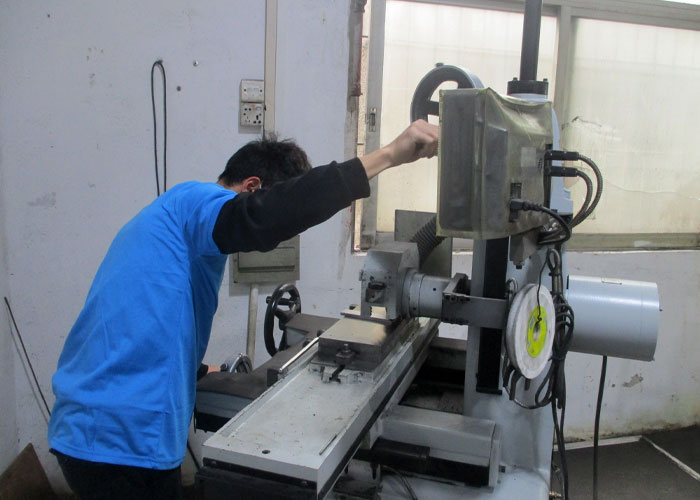
Finishing Services Options
Anodizing
Anodizing helps to resist corrosion, increase surface hardness, improve resistance to wear. This process serves both functional and cosmetic purposes. There are two main types of anodizing:
Type II anodizing is mainly used to produce parts with a uniform, aesthetically pleasing surface and provides good corrosion and limited wear resistance, and has a wide variety of color dye options. The typical coating thickness: 12-18 μm for black, 8-12 μm for clear, 4-8 μm for color.
Type III anodizing also known as hard anodizing, provides excellent corrosion and wear resistance, suitable for functional applications, but is more limited in color—often clear or black only. The typical thickness 30-125 μm.
Vacuum Metalizing
Vacuum metalizing is a form of physical vapor deposition (PVD), a process of combining metal with a non-metallic substrate through evaporation. Layer thicknesses are typically a few microns and a range of finishes are possible. The most common metal used in vacuum metallization is aluminum for a variety of reasons including cost, thermodynamic, and reflective properties.
Metal Plating
Plating is a metal finish that involves coating a metal part with a very thin layer of another metal or metal alloy, in order to protect from corrosion and oxidation of the base part, or to change its cosmetic appearance. Tin, Nickel, Zinc (galvanizing), and Chrome are all common plating metals.
Powder Coating
Powder coating adds a thin layer of protective polymer on the surface of the part. It uses corona discharge phenomenon to make powder coating adsorbed on the workpiece, which is a strong, wear-resistant finish. The typical thickness varies from approximately 50 μm up to 150 μm.
Printing & Etching
You can print custom text and logos on the parts. Silk screening can be used for larger surfaces and when mixing multiple colors for even more complex graphics; Pad printing can be used for printing on curved surfaces; Laser etching is ideal for making precise and permanent marks on metal and and some plastics.
Quote Now to Start Your CNC Machining Project
Complete CNC machining services from prototype to production ensure high quality, fast delivery and competitive prices.