Service
Precision Wire EDM Services, One-Stop & On-Demand
JX facilitates you to order your custom high-performance and top-quality wire EDM parts at low prices. Our wire EDM machines are designed to enhance the operations, efficiency, and performance of all types of parts required by you.
Our facility is climate-controlled and ensures consistency and exactness in every wire EDM cut and every part. JX feature technologically enhanced wire-cut EDM machines. These exceptional wire EDM machines have the ability to machine parts in an extremely accurate way and with high cutting speed while maintaining powerful process control. Moreover, we can achieve dimensional accuracy of +/-0.01mm with precision.


Why Choose Our Precision Wire EDM Services?
Common Metals for Wire EDM Services
Virtually any material that is conductive is a perfect one for wire EDM, and it includes all the metals. JX’s wire-cut EDM equipment also can machine plastic, metal alloys, exotic and precious metals. Below are some most common options.
The surface of the alloy steel is subjected to extremely high temperatures, causing it to melt or evaporate. With wire EDM, you can obtain steel parts with a satisfactory service life. Alloy steel is wear resistant which prevents/eliminates the possibility of accidental imperfections on its surface.
The most interesting thing about wire EDM that it can produce complex shapes out of almost any electrically conductive material, specifically stainless steel. Machined stainless steel parts mostly a part of the aerospace, automotive, surgical fields.
Aluminum is the most common conductive material for wire EDM that can be cut into a precisely accurate part. Aluminum machined parts are mostly appreciated in various engineering applications that thrive for stiffness and high strength in parts. Moreover, the use of aluminum as a wire-cut EDM material is expanding in the aviation, automotive, and marine industries.
It is a good material for wire-cut EDM and is known for its properties that ease the machining process. It’s an alloy of copper and zinc but does not resist wear. JX uses industrial-grade brass to achieve precision in wire EDM machined parts.
Bronze is highly electrically conductive that can be machined successfully with wire EDM in cost-effective manners. Through JX, you can achieve perfect surface finishing and coating for your perfectly machined custom bronze parts. Bronze can improve safety and be effectively machined to obtain optimum results.
Copper and its alloys can be perfectly machined through wire EDM—applications including electrical contact and electrode feature copper as the base material for relative parts. Moreover, copper is cost-effective material, and JX’s selection of the best industrial-grade copper will result in high-performance and quality copper parts.
Iron can be efficient and productive for you, and it offers numerous structural and physical advantages over many other wire EDM materials, including steel and aluminum. Wire EDM has the ability to improve your iron parts’ performance and quality.
Nickel alloys are resistant to high temperatures and corrosion and hard to machine because they harden rapidly. Nickel generates heat when being cut. However, due to its high shear strengths, it offers high resistance to metal removal. Wire EDM is proven perfect for machining nickel parts.
It is one of the most required materials for wire EDM and also the best for airplane or heavy-duty medical equipment. It offers high resistance against aggressive environments. JX’s selection of industrial-grade titanium is a guarantee high-quality parts that last longer and provide better performance and results than other materials.
黄金等奇异材料很难加工,但使用电火花线切割机加工起来非常容易。它有助于黄金在加工过程中保持其优势和特性,并输出精确准确的结果。金是仅次于铂和钛的第三好的导电材料。
在包括工业和电气在内的现代应用中,铂金被誉为高级零件的理想材料。它具有高导电性,这使其非常适合医疗行业的植入式传感器等应用。使用电火花线切割加工这种特殊材料是获得极其精确结果的最佳方式。
Guide To Wire EDM & Buying F.A.Q
Wire Cut EDM has the ability to perform ultraprecision machining of miniaturized parts to extremely powerful solutions for modern machining.
Wire EDM is also known for machining parts with extreme accuracy.
In this FAQ article, you will learn how Wire EDM is an essential part of modern machining to achieve precision parts in a cost-effective manner.
Moreover, you will learn the way JX offers its Wire Cut EDM services to its customers internationally.
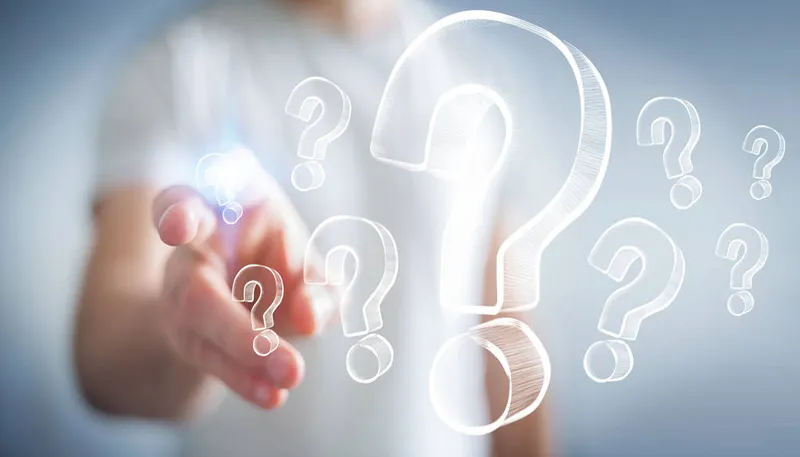

What Is Wire EDM (Wire Cut EDM) Process?
Wire EDM (Electric Discharge Machining) is also popular by the names of wire-cut EDM, cire cutting, wire burning, EDM cutting, and wire erosion.
WEDM cuts or shape a workpiece by using a metallic wire that is a thin electrode wire based on a precision programmed path.
In general, electrode diameters range from 0.004 inches to 0.012 inches (0.10mm – 0.30mm).
However, larger or smaller electrode diameters also achievable with Wire EDM.
No contact between the cutting wire and the workpiece is what gives the wire-cut DEM cutting process uniqueness.
The Wire EDM process starts by rapidly charging the wire to the desired voltage while the wire is placed in deionized water.
A spark jumps the gap between the workpiece and the cutting wire and starts melting/shaping it when the correct level of voltage required is maintained.
The deionized water helps to cool and flushing away the small particles or waste from the gap.
The most interesting thing about wire EDM is that the hardness of the material has no effect on the cutting speed of the cutting wire.
The blanking punches and extrusion dies are some of the most common machined parts by wire cut EDM.
How Wire EDM Works?
Wire-cut EDM always cuts through the entire material. In order to start wire machining, the first step is to drill a hole precisely that is dimensionally accurate or simply start from the edge.
On the machining area, each discharge creates an impact on the tool and a crater in the material.
The cutting wire is mostly made of brass/stratified copper, and there is also no mechanical contact between material and electrode.
Moreover, the wire usually has a diameter between 0.1mm – 0.3mm.
Most importantly, extreme complexity is an easy task for wire EDM and able to machine precision parts out of hard conductive materials.
This cutting process is sparking, and in order to reduce sparking from shorting out, a non-conductive fluid/water is also a part of the complete process and also help to remove waste material, and the process continues.


How Accurate And Fast Is Wire EDM?
Wire EDM is known to be extremely accurate and has the ability to manufacture parts rapidly as well as in cost-effective manners.
It can machine any material that is electrically conductive, and that also includes some extremely hard and exotic ones that can be extremely hard to machine otherwise.
Wire EDM is completely programmable, and this gives it the ability to cut intricate and delicate shapes.
Machining parts and achieving complex shapes with wore-cut EDM is one of the most precise machining methods achieved by experienced engineers.
With advanced technology and state-of-the-art wire EDM machines, manufacturing parts rapidly with high precision and high responsiveness is possible.
Some of the followings are what lead to extremely high speed and high precision wire EDM machining:
● Automatic wire-cut EDM processes
● Surface finishing of parts featuring the complex shapes
What Are The Materials For Wire EDM?
Wire EDM can machine precision parts with extremely tight tolerances with the help of industrial-grade material selection.
The following are the core materials wire EDM works with:
This cutting process is sparking, and in order to reduce sparking from shorting out, a non-conductive fluid/water is also a part of the complete process and also help to remove waste material, and the process continues.
● Austenitic Stainless
● Aluminum
● Alloy Steels
● Bronze Alloys
● Brass
● Carbon Steel
● Copper
● Carbide
● Cobalt
● Cubic Boron Nitride (CBN)
● Iron
● Lead
● Martensitic Stainless
● Magnesium
● Nickel
● Stainless Steel
● Tool Steel
● Titanium
● Tin

What Are The Advantages Of Wire EDM?
Wire EDM offers many exceptional advantages that make it the easiest and most convenient machining process for manufacturing precision parts.
Its high precision allows it to machined parts with extremely complex shapes without facing any problem or error.
Its ability to work with industrial-grade hard materials means it can achieve tighter tolerances as required.
Wire EDM’s ability to handle the high level of part complexity also means that it also can machine extremely small and intricate parts.
Additionally, the following are some core advantages of using wire EDM:
● Excellent surface finish
● Cost-effective and highly efficient
● A high degree of accuracy
● Accurate, predictable, programmable, and repeatable
● Utilizes a relatively compact workspace
● Suitable for hardened/exotic materials
Most importantly, wire EDM also eliminates the possibilities of distortion arising from post-machining processes.
Furthermore, it allows machining of features that would be extremely difficult or nearly impossible using conventional machining methods.

What Are The Applications Of Wire EDM?
Wire EDM is common in die and mold manufacturing processes and has also proven extremely productive in everything from prototyping to full-volume production.
Industrial, engineering, or similar applications that require low levels of residual stress have the most use of wire EDM technology.
Moreover, it is also a great option for manufacturing metal parts and tools.
Most importantly, the most parts wire EDM works with are related to the automotive, aerospace, and electronics industries.
It is also an ideal option for delicate/small parts, thick parts that require extreme precision, and complex shapes.
It’s also proven extremely useful when it comes to machining parts related to medical and surgical.
What Are The Differences Between Wire EDM And Laser Cutting?
Machining speed and accuracy are two things that define both wire EDM and laser cutting.
Laser cutting is faster than wire EDM but can’t achieve accuracy and precision in part machining.
On the other hand, wire EDM is more accurate than laser cutting and also can achieve tighter dimensional tolerances.
Furthermore, wire EDM also handles part complexity with more care, and its services are most preferred in similar cases.
However, laser cutting and wire EDM machines are similar in many ways but, laser cutting features gases and electricity to produce a thermal beam that cuts the material through melting.
However, wire EDM utilizes a super-thin, heated electric wire to cut materials.
In the case of wire EDM, materials must be conductive and tighter tolerances of +/-0.025mm is achievable.


What Are The Differences Between Wire EDM And Sinker EDM?
The primary difference between wire EDM and sinker EDM is the type of electrode used.
Wire EDM uses wire as the electrode that can either be of brass or zinc-coated.
On the other hand, sinker EDM sinks the shape that is on the electrode partway into the workpiece.
Most importantly, wire-cut EDM and sinker EDM both works on the principles of electrical discharge machining.
Sinker EDM has the ability to start machining at any point on the material, but the wire EDM needs to start machining from the material’s edges.
Wire EDM is an exceptional machining process for two-dimensional cutting, and Sinker EDM can handle complex 3D and intricate shapes.
Quote Now to Start Your CNC Machining Project
Complete CNC machining services from prototype to production ensure high quality, fast delivery and competitive prices.